SPbPU has developed artificial skin for robots
Scientists from Peter the Great St. Petersburg Polytechnic University have created a prototype of a tactile sensor for industrial robots. The development will help robots better feel objects during grasping and other manipulations. Data from the «artificial skin» sensors will allow industrial robots to feel the structure of objects and control the force of compression. The work was supported by the Priority-2030 Strategic Academic Leadership Program.
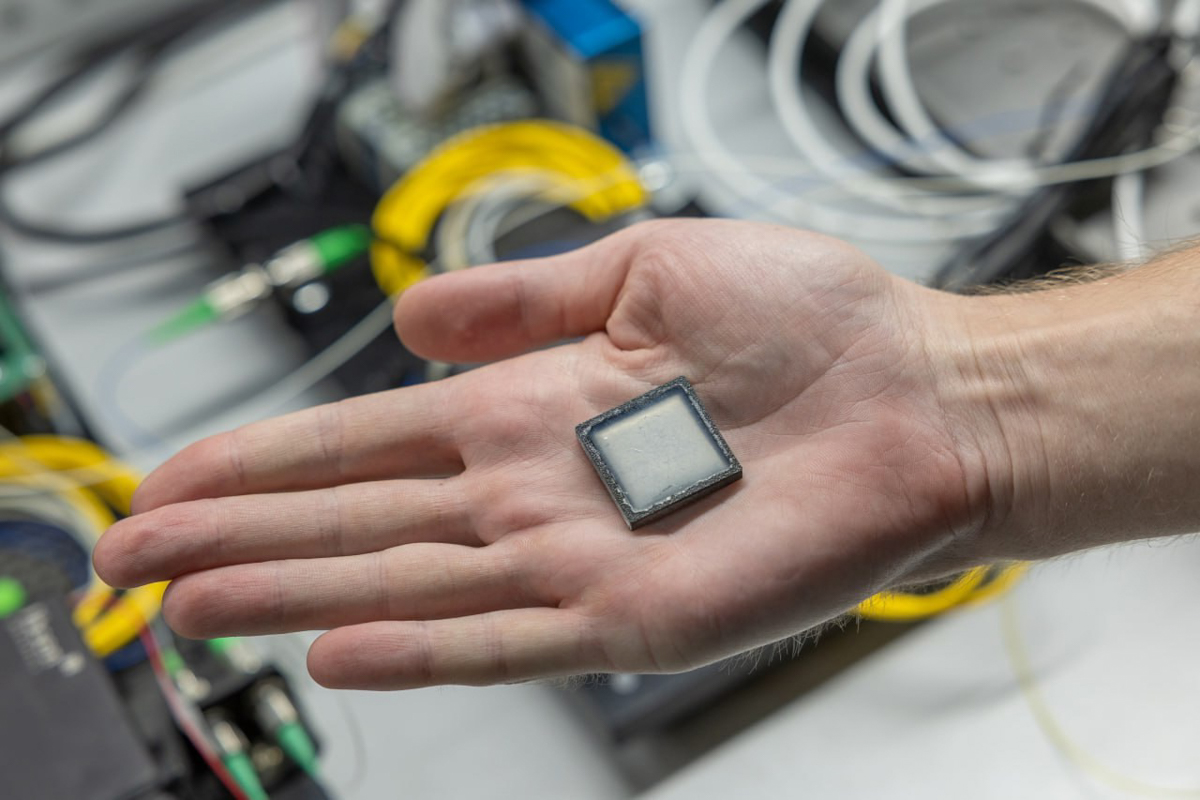
The number of industrial robots is constantly growing every year. Manipulators assemble cars and weld parts, sort goods in the warehouses of large marketplaces, mix compounds in chemical laboratories, and even help surgeons perform most sophisticated robot-assisted operations. Engineers are constantly improving the robot’s skills. One of the directions of such improvements is to create an analog of human systems that will minimize the operator’s participation in the robot’s work.
SPbPU scientists have developed a prototype of a tactile sensor for industrial robots. In essence, it is an «artificial skin» that allows the machine to touch the structure of objects and the strength of its impact on them, which makes them more versatile and accurate relative to their analogs.
The development of such sensors is now being practiced all over the world. The peculiarity of the approach proposed in Polytechnic University is the use of fiber-optic sensitive sensors, which are not susceptible to electromagnetic interference, radiation, and have increased survivability in aggressive external conditions. According to the project leader, Associate Professor of the Graduate School of Applied Physics and Space Technologies of SPbPU Nikolay Ushakov, Doctor of Physics and Mathematics, the use of fiber-optic sensors is of particular interest in such areas as medicine, oil and gas sector, nuclear industry. Also, such sensors simplify the technology of manufacturing the final product and reduce the cost of the product.